Success Story
Technical Documentation under Control
MTU Aero Engines successfully uses the CAFM solution from AT+C EDV GmbH
Marc Hankmann
IT Journalist at Wordfinder Ltd. & Co KG in Hamburg
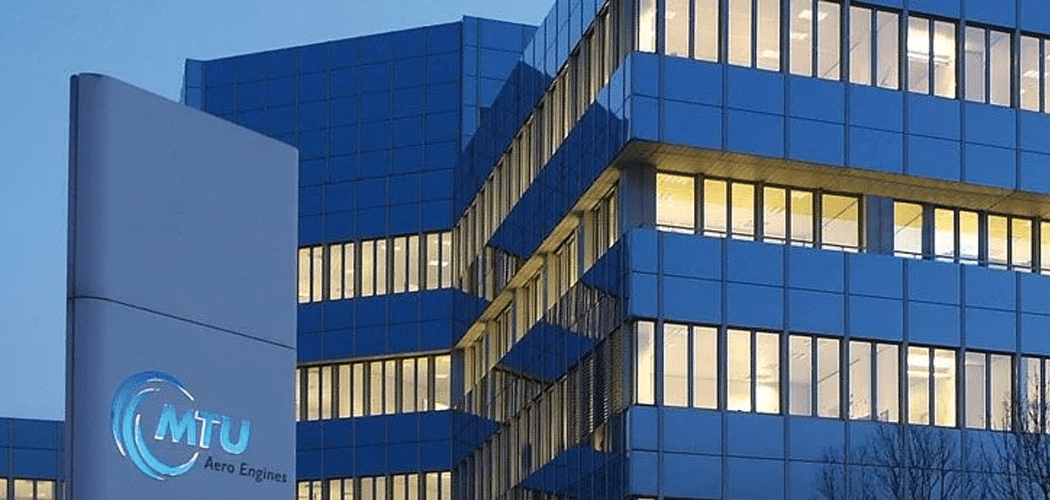
Success Story
Technical Documentation under Control
MTU Aero Engines successfully uses the CAFM solution from AT+C EDV GmbH
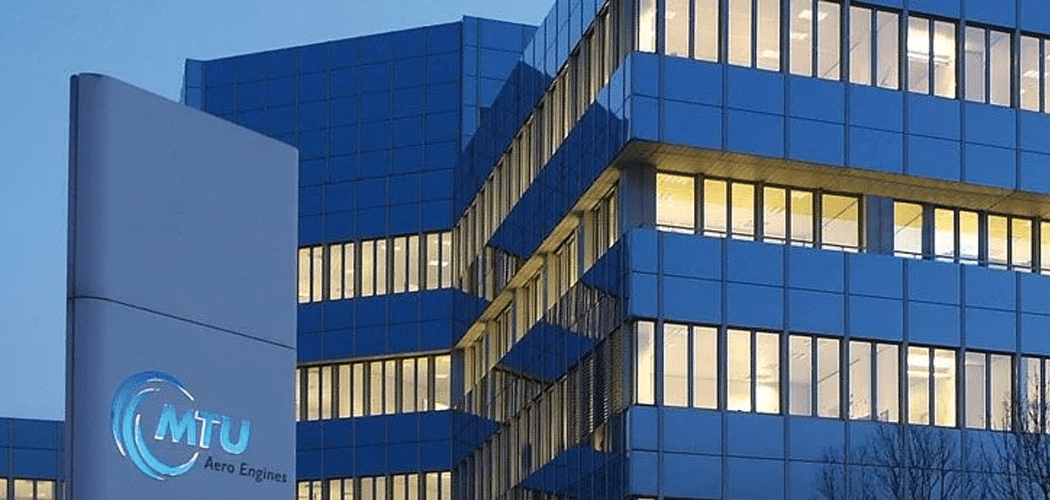
Object data management and key management with AT+C VM.7
When employees walk through the factory hall with oversized CAD plans and search in vain for a connection box, or rooms cannot be found because the wrong room numbers have been entered, the problem is incomplete and incorrect documentation. To avoid such scenarios and speed up processes, MTU Aero Engines uses an IT solution for technical documentation.
The company employs around 9,000 people worldwide. The Munich-based company is one of the top five civil engine maintenance companies. The company counts around 150 airlines among its customers. Documentation in the area of communications technology and LAN infrastructure at the headquarters in Munich, with around 4,700 employees, was partly done in Microsoft Office, partly in paper plans and handwritten notes. This could lead to duplicate or even contradictory information, because employees could not check the documented object data against each other. It has happened before that the plan called for one and the same telephone to be connected to two different connections, says Stefan Meyer, IT planner for Industrial IT at MTU, as an example. Another incident: fitters had to use a DIN A0 hall plan as a guide because the object data was not linked to the existing CAD system. To avoid this in the future, MTU looked for a CAFM solution that could be integrated into the existing IT landscape and would also serve as a location database for the various IT systems. Each IT system has different location information for one and the same object. The risk of error multiplies with the number of systems when employees enter this type of location information manually in the various IT systems without being able to double-check the data.
Replacement of an in-house development
Historically, MTU had previously used a self-developed space management solution based on the Siemens PLM software NX. Due to the positive experience with an IT infrastructure documentation solution, MTU commissioned AT+C GmbH to create a migration concept to replace the old system. The new system was to enhance the advantages that result from using AutoCAD as a quasi-standard for CAD software in the construction sector with special functions for space management. The replacement was also intended to exploit synergy effects that result from cross-departmental use of the software and the shared database.
As a result, the decision to use AT+C VM.7 was very easy for us, as the functionality offered fully covered our requirements and the combination of FM and infrastructure documentation met our expectations exactly, says Stefan Meyer. In addition, the existing data set could be imported almost completely, thus minimizing the effort required for migration. As part of the project, VM.7 became the leading system for space data. However, the data is also offered to other applications via standardized interfaces, which allows the design of cross-application processes, explains Stefan Burger, project manager at AT+C.
Automatic plausibility check
In addition to centralized data storage, the software also provides an automated, urgently needed plausibility check. If, for example, a telephone is assigned to a connection, this assignment can be changed, but the telephone cannot be connected to another connection. The solution also represents cross-object relationships, so that Stefan Meyer and his employees can follow the entire path of an object such as a telephone via the connection box, the floor and building distributor, and up to the telephone system. In addition, fitters can put aside the cumbersome, large CAD plans, because they now receive all important object data directly from the CAD system via the software.
In addition, MTU also manages its keys with AT+C's Key Manager. What sounds quite banal at first is understandable when you know that MTU has to manage over 50,000 keys and of course not every employee is allowed access to the military area, for example. Previously, a number of manual steps were necessary to assign keys. With the Key Manager, MTU now benefits from automated personnel import, for example, so that personal data no longer has to be collected and stored manually. MTU also uses this automatic assignment of personnel and object data for telephone documentation. The system assigns each device to a person with the corresponding location data. The route search is also fully automatic, adds Meyer. This means that every technician can immediately recognize the optimal route in terms of circuit technology via the graphical interface. Here, too, the plausibility check plays a decisive role, because a switching point or switching pin can only be assigned once.
Realistic representation of the server cabinets
MTU is currently working on linking the solution with network and asset management. In network management, for example, information about the configuration of the server cabinets is stored. VM.7 automatically takes this information and realistically displays the configuration of the server cabinets. Previously, such information had to be recorded manually. Conversely, asset management receives more detailed information about individual objects via the software. An employee no longer has to search the entire side of a factory hall for the right connection socket in order to find the appropriate hardware, explains Stefan Meyer.
MTU is currently only using the FM solution in Munich. The Key Manager is also used at the second largest location in Hanover. Meyer assumes that other locations in the group will follow suit. Apart from that, MTU plans to include all production facilities in the solution at the Munich location and link these facilities to SAP using inventory numbers.
Author: Marc Hankmann
Image source: MTU Aero Engines AG
Object data management and key management with AT+C VM.7
When employees walk through the factory hall with oversized CAD plans and search in vain for a connection box, or rooms cannot be found because the wrong room numbers have been entered, the problem is incomplete and incorrect documentation. To avoid such scenarios and speed up processes, MTU Aero Engines uses an IT solution for technical documentation.
The company employs around 9,000 people worldwide. The Munich-based company is one of the top five civil engine maintenance companies. The company counts around 150 airlines among its customers. Documentation in the area of communications technology and LAN infrastructure at the headquarters in Munich, with around 4,700 employees, was partly done in Microsoft Office, partly in paper plans and handwritten notes. This could lead to duplicate or even contradictory information, because employees could not check the documented object data against each other. It has happened before that the plan called for one and the same telephone to be connected to two different connections, says Stefan Meyer, IT planner for Industrial IT at MTU, as an example. Another incident: fitters had to use a DIN A0 hall plan as a guide because the object data was not linked to the existing CAD system. To avoid this in the future, MTU looked for a CAFM solution that could be integrated into the existing IT landscape and would also serve as a location database for the various IT systems. Each IT system has different location information for one and the same object. The risk of error multiplies with the number of systems when employees enter this type of location information manually in the various IT systems without being able to double-check the data.
Replacement of an in-house development
Historically, MTU had previously used a self-developed space management solution based on the Siemens PLM software NX. Due to the positive experience with an IT infrastructure documentation solution, MTU commissioned AT+C GmbH to create a migration concept to replace the old system. The new system was to enhance the advantages that result from using AutoCAD as a quasi-standard for CAD software in the construction sector with special functions for space management. The replacement was also intended to exploit synergy effects that result from cross-departmental use of the software and the shared database.
As a result, the decision to use AT+C VM.7 was very easy for us, as the functionality offered fully covered our requirements and the combination of FM and infrastructure documentation met our expectations exactly, says Stefan Meyer. In addition, the existing data set could be imported almost completely, thus minimizing the effort required for migration. As part of the project, VM.7 became the leading system for space data. However, the data is also offered to other applications via standardized interfaces, which allows the design of cross-application processes, explains Stefan Burger, project manager at AT+C.
Automatic plausibility check
In addition to centralized data storage, the software also provides an automated, urgently needed plausibility check. If, for example, a telephone is assigned to a connection, this assignment can be changed, but the telephone cannot be connected to another connection. The solution also represents cross-object relationships, so that Stefan Meyer and his employees can follow the entire path of an object such as a telephone via the connection box, the floor and building distributor, and up to the telephone system. In addition, fitters can put aside the cumbersome, large CAD plans, because they now receive all important object data directly from the CAD system via the software.
In addition, MTU also manages its keys with AT+C's Key Manager. What sounds quite banal at first is understandable when you know that MTU has to manage over 50,000 keys and of course not every employee is allowed access to the military area, for example. Previously, a number of manual steps were necessary to assign keys. With the Key Manager, MTU now benefits from automated personnel import, for example, so that personal data no longer has to be collected and stored manually. MTU also uses this automatic assignment of personnel and object data for telephone documentation. The system assigns each device to a person with the corresponding location data. The route search is also fully automatic, adds Meyer. This means that every technician can immediately recognize the optimal route in terms of circuit technology via the graphical interface. Here, too, the plausibility check plays a decisive role, because a switching point or switching pin can only be assigned once.
Realistic representation of the server cabinets
MTU is currently working on linking the solution with network and asset management. In network management, for example, information about the configuration of the server cabinets is stored. VM.7 automatically takes this information and realistically displays the configuration of the server cabinets. Previously, such information had to be recorded manually. Conversely, asset management receives more detailed information about individual objects via the software. An employee no longer has to search the entire side of a factory hall for the right connection socket in order to find the appropriate hardware, explains Stefan Meyer.
MTU is currently only using the FM solution in Munich. The Key Manager is also used at the second largest location in Hanover. Meyer assumes that other locations in the group will follow suit. Apart from that, MTU plans to include all production facilities in the solution at the Munich location and link these facilities to SAP using inventory numbers.
Author: Marc Hankmann
Image source: MTU Aero Engines AG